by Dr. Mohamed M. Abdol Quader
6 minutes
QC Laboratory at a Glance: Part 1
Explore the essential role of Quality Control in pharmaceuticals, from testing procedures to ensuring drug efficacy and safety.
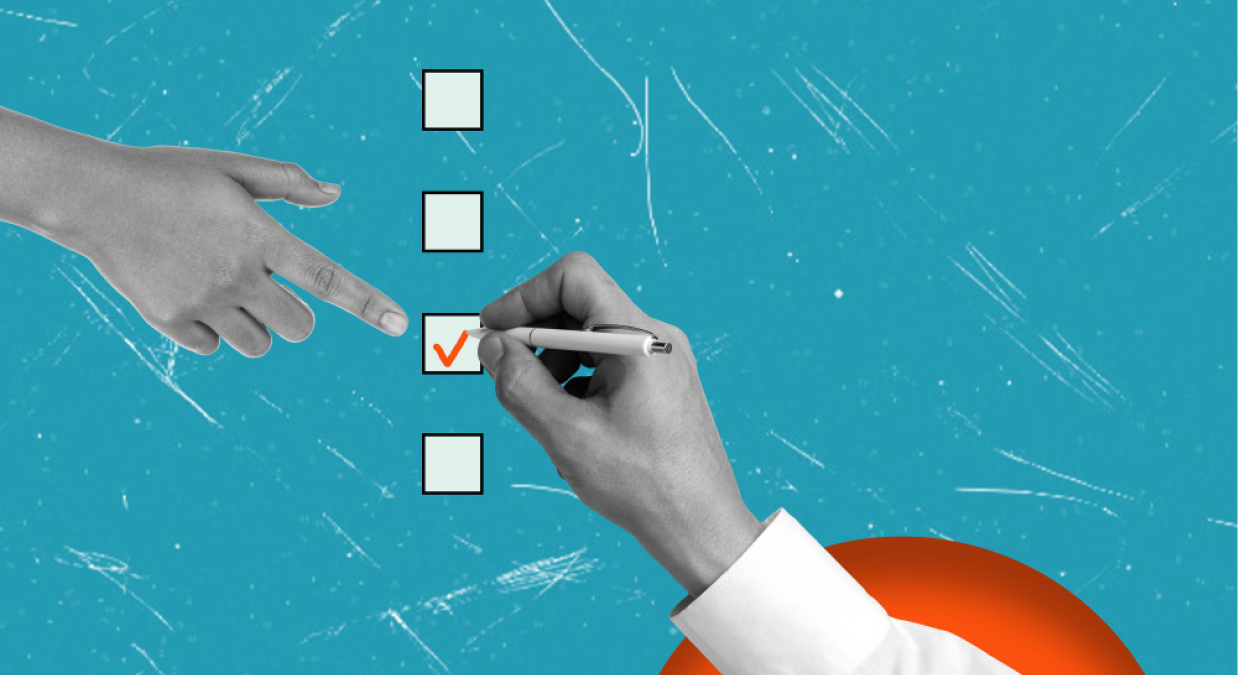
Normally, as a Quality Control "QC" professional you can predict the stressful style of your work! That is because you are the cornerstone in the "conform-nonconform" cycle for all production inputs and outputs which is the base of the "drug product release-rejection" process.
What is the QC role? Why is QC so important? How does QC laboratory perform and fit to the manufacturing facility system? Finally, how to manage the total view of QC and avoid mistakes in the laboratory affecting instruments, performance or accuracy? Those points and interesting details to be covered in this concise series of 3 articles entitled: "QC laboratory at a glance".
What is the QC role?
Basic knowledge
Basically, we should know that any regulations or standards for the pharmaceutical products aim to achieve: the efficacy, safety and quality triangle (see Fig. 1). So, the QC overall target is to check the achievement of the 3 requirements. This role comes, routinely, through laboratory testing of samples. What are samples to be tested? Simply, all production inputs and outputs to be tested, unless justified to be waived! What tests are required? This is to be discussed below.
Samples of QC
As shown in Fig. 2-a and Fig. 2-b, the inputs and outputs of production which need to be samples for analysis at QC laboratory are, nearly, all things you can imagine! Starting from: air (environmental monitoring), till the active and inactive materials forming the drug product and passing by water for pharmaceutical purposes.
Categories of tests
As shown in Fig. 3, the categories covering tests of QC can be summarized into 3 categories: physical, chemical and microbiological. All tests are not needed for all samples. Guidelines, pharmacopeias and standard operating procedures (in- house instructions) define the required testing per each sample type. For example: water samples need to achieve microbiological criteria and, if needed for sterile production, it needs achieving sterility "freedom from viable microorganisms" and absence of pyrogens "the non-viable fever-producing materials". Also, it should achieve physicochemical properties such as definite pH range, conductivity and freedom form hardness (calcium and magnesium ions). Another example is the testing of environment, which is conducted through, only, microbiological point of view by distributing specific plates at the production area to detect the microbial count or sterility (according to the class of the area). One of the most important examples is the analytical testing of the drug product itself, its components (raw materials) and its semi-finished product(s) (in- process samples). This last example will be discussed in detail.
Universal vs. "dosage form"-relevant tests
Analytical procedures applied to the active pharmaceutical ingredients, excipients, semi- finished and finished products can be categorized into: universal and "Dosage form"- relevant tests.
Before we go to the tests, we need to know what is meant by each of the mentioned expressions. A "dosage form", simply, is the final form of the drug which will be administered to the patient. The active pharmaceutical ingredient is the drug responsible for the therapeutic action. The excipients are the complementary materials providing a matrix for the drug itself, to facilitate its manufacturing, enhance its properties and/ or stabilize it. Finally, the semi- finished product is a drug mixed with one or more excipient(s) but not reached to the stage of being a finished product which the patient can receive.
Dosage forms may be solid (as: tablets, capsules and powders), liquids (as syrups, suspensions and emulsions) or semi solids as (gels, creams and ointments).
Regarding semi- finished product we can understand its concept when following an example of tablet manufacturing flow chart (Fig. 4):
So, now we can go to predict which universal tests should be done for a sample e.g. finally packed product (FFP) of Paracetamol tablet. If you were in a patient`s place, which testing would you predict that QC laboratory should conduct? Imagine that the tablets of Paracetamol, by mistake, have another API! Continue to imagine and suppose that a pregnant woman has taken those tablets and it contains another drug with high teratogenicity! First of all, IDENTIFICATION TESTING is required, so we are confident that the tablets contain the right API, in our example: "Paracetamol". It is an important shield of safety. Secondly, we need ASSAY to ensure that the amount of API is as labeled, so that the patient takes his right dose. Moreover, assay of preservatives and antioxidants in case of a liquid product. A third test is very important and can be deducted also by your imagination. Imagine that the tablets during compression suffered from a high variability in weight and/ or API content, the patient will suffer also from variability in effect! Some tablets may give an effect higher than required, may be with higher side effects or even with toxic effects in case of narrow therapeutic index drugs, and other tablets give very weak effects or even no effect. Accordingly, UNIFORMITY OF DOSAGE UNIT is an essential test and has more technical details that QC professionals are aware of. So, ASSAY AND UNIFORMITY OF DOSAGE UNIT tests ensure efficacy and safety. Another fourth test is very critical and important for the safety of patients, the IMPURITIES test. Impurities are substances, not required in the drug product, that come to the drug product (as residuals from organic solvent used in manufacturing) or come from the drug (as degradation substances from the API). Some other types of impurities need evaluation and/ or control but not to be discussed in this simplified article (e.g., elemental impurities). Fifth universal test may be alcohol content in case of liquid formulation containing alcohol. Finally, a microbiological examination should be conducted to ensure neither pathogenic strain nor high amounts of bacterial/ fungal contamination are found.af
Now, after we mentioned the universal tests required. What are the "dosage forms"-related tests? In the next article we should highlight examples of such tests.
?Could the QC role stand alone to assure quality of the product
Actually, a QC role is not enough for complete assurance of quality! Simply, If I depended only on QC samples to assure quality, it is a big mistake. We need a QUALITY ASSURANCE (QA) department to follow the process details itself. The total view of the production process, documentation cycle and total quality management are the role of QA with is the responsible department for release of the product after complete review of the QC certificates, production processes, in-process control and documents, it is also the responsible person of the final decision of product rejection in case of QC reported out of specifications.
Worthy to mention the famous approach called QUALITY BY DESIGN (QbD) which aims to insert the quality as an embedded composition in the manufacturing process through an extensive exercise of designing product, so that quality in this approach is not depending on "testing" but on "designing" from at start of the manufacturing cycle.
Is the QC role important?
Finally, after this short highlighting of the QC role, we can appreciate this great role which supports the efficacy and safety of the product under the umbrella of quality standards.
In the next article, we will have detailed examples from different dosage forms and tests to be conducted suitable to each dosage form. Stay tuned!