by Michael Bani
5 minutes
How to Lead in Pharma: Mr. Marco's Insights on Management & Technology
From Voices of Innovation | Pg 24
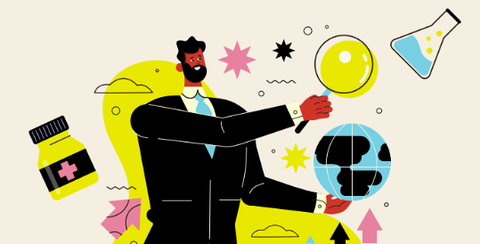
About Mr. Marco Macazzola
Mr. Marco, a seasoned pharmaceutical professional, shares his journey from a laboratory analyst to a plant manager, emphasizing operational excellence, technology adoption, and sustainability. He discusses challenges like regulatory compliance, supply chain management, and crisis resolution, highlighting initiatives such as electronic systems, innovative technologies, and environmental strategies. He advises aspiring plant managers to engage hands-on with industry processes and stresses the importance of continuous learning to adapt to evolving industry trends.
Pharma Now: Can you share your journey in the pharmaceutical industry and what led you to become a plant manager?
Mr. Marco: I started in the pharmaceutical industry over 20 years ago as a laboratory analyst. I then held various management positions in quality control and quality assurance. In 2023, I was given the opportunity to take on the position of Site Director, covering a business function. Over the years, I have been able to learn and deepen important concepts of GLP and GMP, which I consider fundamental in making strategic decisions for the company.
Pharma Now: What are some key milestones and achievements in your career that you are particularly proud of?
Mr. Marco: I have been particularly proud to have been given the opportunity to manage several groups within Quality and now a fantastic cross-departmental team. On a personal note, I am very proud to have been involved in FDA inspections with no comments and to have established a very good relationship with the agency.
Pharma Now: What does operational excellence mean to you, and how do you achieve it at your facility?
Mr. Marco: For me, operational excellence is the basis for ensuring the quality of the medicines we produce. Every day, we think with the team about what can be improved quickly and effectively.
Pharma Now: Can you describe a recent initiative or project that significantly improved operational efficiency?
Mr. Marco: While respecting the specific characteristics of our products, we are integrating single-use technologies into our production system to minimise the associated risks and ensure greater efficiency. We also evaluate the sustainability of the companies we work with.
Pharma Now: How do you ensure that your plant consistently meets quality standards and regulatory compliance?
Mr. Marco: The readiness of the plant is guaranteed by a continuous monitoring system, which facilitates the release of our batches thanks to pre-established critical control points and quality monitoring.
Pharma Now: What are the key challenges you face in maintaining high-quality production, and how do you address them?
Mr. Marco: Over the past 20 years, the application concepts based on the requirements of 21 CFR part 11 have challenged the plants where I have worked to continually change from paper-based systems to electronic systems capable of meeting ALCOA+ principles as well as ensuring independent and effective controls.
Pharma Now: How is technology transforming pharmaceutical manufacturing at your plant?
Mr. Marco: By replacing paper forms with electronic forms in all areas of the plant, we have reduced costs by reducing downtime for approval and consultation steps, and consequently improved productivity. From a GxP perspective, the robustness of the data and ALCOA+ requirements has been increased and the risk of error reduced.
Pharma Now: Can you share examples of innovative technologies or processes that have been implemented recently?
Mr. Marco: In our plant, we are transforming the system to acquire data. Some examples are the Scada system, Environmental Monitoring tracking system, and we are planning to implement the Electronic Batch Record next year.
Pharma Now: How do you manage supply chain challenges, especially in terms of raw material procurement and inventory management?
Mr. Marco: Diversification into centralised supply chains has enabled our business continuity to remain robust.
Pharma Now: What strategies do you use to mitigate supply chain risks?
Mr. Marco: By selecting and qualifying different suppliers for key materials from different countries.
Pharma Now: What initiatives have you implemented to reduce the environmental impact of your manufacturing processes?
Mr. Marco: The challenge of reducing the environmental impact of our manufacturing processes is very important to us. We have addressed a number of factors that have an impact on the use of injection water and reducing the energy required at the times when it is possible, optimizing HVAC systems for maximum efficiency.
Pharma Now: How do you balance sustainability goals with production efficiency?
Mr. Marco: We strike the right balance by carefully selecting our suppliers. For example, one of our new suppliers, Lugaia, not only allows us to reduce our use of water and detergents but also has sustainability and respect for the environment as part of its corporate mission.
Pharma Now: How do you ensure that your workforce is skilled and adequately trained to meet the demands of pharmaceutical manufacturing?
Mr. Marco: The growth path of our personnel requires several steps to be qualified and qualified for the key functions of our plant. Working side by side with more experienced people, I find that there are many moments of daily work where I am a winner.
Pharma Now: What strategies do you use to foster a culture of continuous improvement among your staff?
Mr. Marco: I believe that continuous improvement is a concept that needs to be instilled in the minds of all employees every day. To do this, in every meeting that is held in our factory, we challenge ourselves to understand how to track this improvement.
Pharma Now: Can you discuss a time when your plant faced a significant crisis and how you managed it?
Mr. Marco: I have worked in several production sites and, as you can imagine, there have been several moments of crisis, some of them involving technical aspects. The management of the technical aspects required the commitment of a multifunctional team involving the SME of the particular aspect, but not only that: in these cases, you have to correctly transmit information through the distribution chain in order to analyze the best strategies together with the commercial partners.
Pharma Now: What measures do you have in place to ensure resilience and continuity in operations during unforeseen events?
Mr. Marco: We have a continuous monitoring programme of key parameters to detect abnormal trends.
Pharma Now: What emerging trends do you see in pharmaceutical manufacturing, and how is your plant preparing to address them?
Mr. Marco: In the pharmaceutical industry, and in particular in the manufacture of injectable drugs, new technologies such as artificial intelligence for visual inspection of products or goggles for remote visualisation during audits are being introduced at a faster pace than in the past.
Pharma Now: How do you foresee the future of pharmaceutical manufacturing evolving over the next decade?
Mr. Marco: I believe that over the next decade, artificial intelligence will increasingly enter the modulation of pharmaceutical production control processes.
Pharma Now: What advice would you give to young professionals aspiring to become plant managers in the pharmaceutical industry?
Mr. Marco: What I recommend is to touch things. Nowadays we learn to use 'closed boxes'. For me, it is important that people know the contents of these 'boxes' and this can be done by going out into the field, seeing, and 'touching'.
Pharma Now: How important is continuous learning and staying updated with industry advancements for success in this field?
Mr. Marco: Continual learning and keeping abreast of industry developments is essential as the nature of the work we do on a daily basis is constantly evolving, for example in the field of biotechnology.