by Mrudula Kulkarni
7 minutes
Primary packaging in pharmaceutical Materials and Technologies
Primary pharmaceutical packaging protects drugs from contamination, degradation, and damage. Explore key technologies, challenges, and future trends.
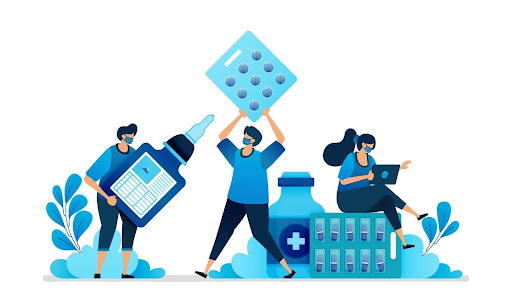
Primary pharmaceutical packaging refers to the materials and technologies used to directly encase and protect pharmaceutical products from contamination, degradation, and damage during storage, handling, and transportation. This article discusses the key technologies used in primary packaging, the challenges faced, and the primary functions of these packaging materials. Additionally, we provide insights into the future of primary packaging materials and technology and answer a few frequently asked questions. Dive deeper to learn more!
How Does Primary Packaging Protect and Contains Pharmaceutical Products?
Primary pharmaceutical packaging is the frontline defence in preserving medication quality, safety, and efficacy. Its primary role is to protect and contain pharmaceutical products from the point of manufacture to the end-user. In this section, we understand the critical functions of primary packaging and appreciate how it safeguards the health and well-being of patients worldwide.
a. Protection from Environmental Factors
One of the paramount functions of primary pharmaceutical packaging is to shield the product from various environmental factors. These include:
- Moisture: Many pharmaceutical products are sensitive to humidity, which can cause degradation or chemical reactions that render the medication ineffective. Packaging materials like blister packs, glass vials, and certain plastics provide an impenetrable barrier to moisture.
- Light: Certain medications, especially those containing light-sensitive compounds, require protection from light exposure to maintain their stability. Amber-coloured glass bottles and opaque plastic containers are commonly used to protect such drugs from photodegradation.
- Oxygen: Exposure to oxygen can lead to oxidation reactions that compromise the integrity of pharmaceuticals. Packaging technologies that utilise vacuum sealing or the inclusion of oxygen absorbers help mitigate this risk.
b. Prevention of Contamination
Primary packaging acts as a sterile barrier, preventing contamination from microorganisms, dust, and other particulates. This is particularly crucial for injectable drugs, which must be free from contaminants to ensure patient safety. Using aseptic packaging processes and materials like sterilised glass ampoules and pre-filled syringes is standard practice in the industry.
c. Physical Protection
Pharmaceutical products must be protected from physical damage during handling, transportation, and storage. Primary packaging materials such as rigid plastics and glass provide the necessary durability to prevent product breakage, crushing, or leakage. This physical protection ensures the medication reaches the patient in its intended form and dosage.
d. Containment and Dosage Accuracy
Primary packaging is also vital for containing and dispensing the correct medication dosage. This is particularly important for liquid medications, injectables, and unit-dose packaging. Innovative packaging solutions like metered-dose inhalers, calibrated droppers, and blister packs ensure that patients receive the accurate amount of medication needed for effective treatment.
e. Enhancing Patient Compliance
User-friendly primary packaging can significantly improve patient compliance with medication regimens. Easy-to-open containers, child-resistant caps, and clear labelling with dosing instructions enhance the product's usability. Blister packs, for instance, allow patients to easily track their medication intake, reducing the risk of missed doses or overmedication.
f. Regulatory Compliance
Primary packaging must adhere to stringent regulatory standards set by bodies such as the FDA and EMA. These regulations ensure that packaging materials are safe and effective and do not interact with the pharmaceutical product. Compliance with these standards is critical for gaining approval to market and sell medications.
Innovative Technologies Used in Primary Packaging
Advancements in primary packaging technologies have significantly enhanced the safety and usability of pharmaceuticals. For instance, blister packaging, which encapsulates individual doses, has become a popular choice for tablets and capsules, offering superior protection and patient convenience. Other innovative packaging solutions include pre-filled syringes, which improve dosing accuracy and reduce contamination risks, and advanced closures with tamper-evident features that enhance security.
a. Blister Packaging
Blister packaging is one of the pharmaceutical industry's most widely used primary packaging technologies. It involves sealing individual doses of medication between a thermoformed plastic cavity and a backing material, typically aluminium foil.
Applications
- Tablets and Capsules for oral solid dosages
- Unit-Dose Packaging to ensure accurate dosing and improve patient adherence by making it easy to track medication intake.
Advantages
- Enhanced Protection: Each dose is individually sealed, reducing the risk of contamination.
- Convenience: Blister packs are user-friendly and portable.
- Tamper Evident: The packaging clearly shows if it has been tampered with, enhancing security.
b. Bottles and Vials
Bottles and vials are traditional but essential primary packaging solutions, especially for liquid and injectable medications. These containers are made from materials such as glass and high-quality plastics.
Applications
- Liquid Medications: Bottles are used for syrups, suspensions, and other liquid formulations.
- Injectables: Vials are commonly used for sterile injectable drugs, ensuring the medication remains uncontaminated until use.
Advantages
- Versatility: Suitable for various formulations, including liquids, powders, and semi-solids.
- Durability: Glass vials offer excellent barrier properties and chemical resistance.
c. Pre-Filled Syringes
Pre-filled syringes are an advanced primary packaging technology designed for injectable medications. They come ready to use, reducing preparation time and minimising the risk of dosing errors.
Applications
- Vaccines and Biologics: Pre-filled syringes are ideal for vaccines, biologics, and other parenteral drugs that require precise dosing.
- Emergency Medications: Their ease of use makes them suitable for emergency treatments.
Advantages
- Dosing Accuracy: Pre-filled syringes ensure that patients receive the exact dose prescribed.
- Reduced Contamination Risk: The closed system minimises exposure to contaminants during administration.
d. Ampoules
Ampoules are small sealed vials made of glass or plastic to contain and preserve a single dose of liquid medication.
Applications
- Injectables: Susceptible drugs that require airtight and sterile conditions.
Advantages
- Sterility: Ampoules provide an excellent barrier against contaminants, ensuring the medication remains sterile until opened.
- Protection: They offer superior protection against external factors such as oxygen and moisture.
e. Strip Packaging
Strip packaging involves sealing individual doses of medication between layers of film or foil, creating a strip of unit doses that can be easily separated.
Applications
- Oral Solid Dosages are commonly used for tablets and capsules, particularly over-the-counter medications.
- Unit-Dose Packaging: Like blister packs, strip packaging ensures accurate dosing and enhances patient compliance.
Advantages
- Portability: Strip packs are compact and easy to carry.
- Hygiene: Each dose is individually sealed, reducing the risk of contamination.
Sachets
Sachets are flexible packets that package single doses of powders, granules, or liquid medications. They are made from various materials, including plastic, foil, and paper laminates.
Applications
- Oral Granules and Powders: Ideal for single-dose oral medications like rehydration salts and dietary supplements.
- Liquid Formulations: Used for single doses of liquid medications and topical creams.
Advantages
- Convenience: Sachets are easy to use and dispose of.
- Portability: They are lightweight and portable, ideal for on-the-go use.
Cartridge Systems
Cartridge systems are cylindrical containers that hold and dispense liquid medications, typically in conjunction with reusable delivery devices like pens or pumps.
Applications
- Insulin Delivery: Widely used in diabetes care for insulin pens.
- Reconstitution Systems: Employed for medications that need to be mixed before administration.
Advantages
- Ease of Use: Cartridges simplify medication administration and are particularly useful for patients requiring frequent injections.
- Reduced Waste: Reusable delivery devices minimise waste compared to single-use syringes.
Challenges in Primary Packaging
Primary pharmaceutical packaging ensures medication safety, efficacy, and integrity. Despite its importance, the industry faces numerous challenges, which are discussed in this section, that impact the development and implementation of effective primary packaging solutions.
Regulatory Compliance
One of the significant challenges in primary packaging is adhering to stringent regulatory standards. Regulatory bodies like the FDA, EMA, and other global agencies set rigorous guidelines to ensure safe and effective packaging materials.
- Complexity: The regulatory landscape has varying requirements across different regions.
- Cost: Compliance can be costly, requiring extensive testing and validation.
- Innovation Constraints: Regulations can sometimes hinder innovation, as new packaging materials and technologies must undergo thorough regulatory scrutiny before approval.
Material Compatibility
Another critical challenge is ensuring that primary packaging materials are compatible with pharmaceutical products. The packaging must not interact with the medication in a way that could compromise its stability, efficacy, or safety.
- Chemical Interactions: Some drugs may react with packaging materials, leading to degradation or reduced potency.
- Leachable and Extractables: Packaging materials can release substances into the medication, potentially affecting its quality and safety.
- Barrier Properties: Finding materials that provide adequate protection against moisture, light, and oxygen while remaining chemically inert can be complex.
Sustainability
The pharmaceutical industry is under increasing pressure to adopt sustainable practices, including in primary packaging. However, balancing sustainability with the need for high-quality, protective packaging presents significant challenges.
- Material Selection: Identifying eco-friendly materials that meet stringent safety and performance requirements.
- Cost Implications: Sustainable packaging materials and processes can be more expensive, posing a financial challenge for manufacturers.
- Regulatory Approval: New sustainable materials must undergo rigorous testing and approval, which can delay implementation.
Patient Compliance
Ensuring that primary packaging enhances patient compliance is a significant concern. Packaging must be user-friendly and accessible to a diverse patient population, including the elderly and those with disabilities.
- Accessibility: Packaging should be easy to open and handle, which can be challenging for patients with limited dexterity or strength.
- Clear Labelling: Labels must be clear and informative to help patients adhere to their medication regimens accurately.
- Tamper-Evident Features: Balancing ease of use with the need for tamper-evident features to ensure safety can be difficult.
Counterfeit Prevention
Counterfeit medications significantly risk patient safety and the pharmaceutical industry's integrity. Primary packaging plays a crucial role in preventing counterfeiting.
- Advanced Security Features: To ensure authenticity, implement holograms, QR codes, and RFID tags.
- Cost and Complexity: Adding security features can increase packaging costs and complexity.
- Keeping Pace with Counterfeiters: As counterfeiters become more sophisticated, packaging technologies must continually evolve to stay ahead.
Technological Integration
Integrating advanced technologies into primary packaging can improve functionality but also presents challenges.
- Innovative Packaging: Incorporating sensors and other intelligent technologies to monitor and communicate the condition of the medication.
- Compatibility: Ensuring that technological components do not interfere with the medication or its packaging.
- Cost and Accessibility: Advanced technologies can be expensive and not feasible for all types of medications or markets.
Future Directions
The pharmaceutical industry and the technologies and materials used in primary packaging are continuously evolving. Innovations such as innovative packaging, which can monitor and communicate the condition of the medication, and sustainable packaging materials are on the rise. This section highlights the advancements that enhance the protection and containment of pharmaceuticals, address environmental concerns, and improve patient engagement.
Innovation in Materials
Developing new materials that offer improved protection, sustainability, and compatibility with pharmaceuticals is a promising direction for the future.
- Biodegradable Plastics: Research into biodegradable and compostable materials that can provide the necessary barrier properties.
- Intelligent Polymers: Materials that can respond to environmental changes, such as temperature or humidity, to protect the medication better.
Enhanced Regulatory Frameworks
Collaboration between regulatory bodies and the pharmaceutical industry can lead to more streamlined and adaptive regulatory frameworks.
- Global Harmonization: Efforts to harmonise regional regulations can reduce complexity and facilitate innovation.
- Adaptive Regulations: Developing regulations that quickly adapt to new technologies and materials.
Advanced Manufacturing Techniques
Adopting advanced manufacturing techniques can enhance the efficiency and effectiveness of primary packaging.
- 3D Printing: Customizable packaging solutions that can be quickly produced and tailored to specific medications.
- Automation: Increased use of automation in packaging processes to improve precision and reduce errors.
Focus on Patient-Centric Design
Designing packaging with the end-user in mind can significantly improve patient compliance and outcomes.
- User-Friendly Features: Developing packaging that is easy to open, handle, and understand.
- Accessibility Innovations: Incorporating features such as braille labels and easy-grip designs to cater to all patients.
Anti-Counterfeiting Technologies
Continuing to develop and implement advanced anti-counterfeiting technologies is essential.
- Blockchain Technology: Using blockchain to create secure, immutable records of the pharmaceutical supply chain.
- Digital Verification: QR codes and other digital verification methods that patients can easily use to verify the authenticity of their medication.
Sustainability
- Focus on Sustainability: The pharmaceutical industry is prioritising sustainable primary packaging solutions.
- Eco-friendly Innovations: Development of eco-friendly materials and processes to minimise environmental impact.
- Biodegradable and Recyclable Materials: The adoption of biodegradable plastics and recyclable materials is increasing.
- Commitment to Sustainability: Reflects the industry's dedication to reducing packaging waste.
Conclusion
As we reach the end of this discussion, it must be clear that the primary packaging of pharmaceuticals is a complex and evolving field, facing numerous challenges, from regulatory compliance and material compatibility to sustainability and counterfeit prevention. However, the future holds promising directions with advancements in materials, regulatory frameworks, manufacturing techniques, patient-centric design, and anti-counterfeiting technologies.
By addressing these challenges and embracing innovation, the pharmaceutical industry can continue to improve the safety, efficacy, and accessibility of medications for patients worldwide. For the latest updates and insights on primary packaging technologies and other developments in the pharmaceutical industry, turn to Pharma Now, your go-to digital magazine, for the latest news in the pharma industry.
FAQs
1. What is primary packaging in pharmaceuticals?
Primary packaging refers to the immediate packaging directly containing the pharmaceutical product, safeguarding it from environmental factors, contamination, and physical damage.
2. What are the essential functions of primary packaging materials?
Primary packaging materials protect the product from external elements such as moisture, light, oxygen, and microbial contamination. They must also be inert, not interacting with the drug in any way that could alter its potency or safety.
3. What are some common primary packaging materials used in pharmaceuticals?
Common primary packaging materials include glass, plastics (such as HDPE), and metal. Each material is chosen based on its specific properties and compatibility with the pharmaceutical product.
4. What are some technological innovations in primary packaging?
Technological innovations in primary packaging include blister packaging, prefilled syringes, advanced closures with tamper-evident features, and intelligent packaging solutions that monitor medication conditions and patient adherence.
5. How does primary packaging contribute to regulatory compliance and user experience?
Primary packaging must adhere to stringent regulatory standards set by bodies like the FDA and EMA to ensure safety and efficacy. User-friendly packaging with clear instructions and easy-to-open features enhances patient compliance and overall user experience.